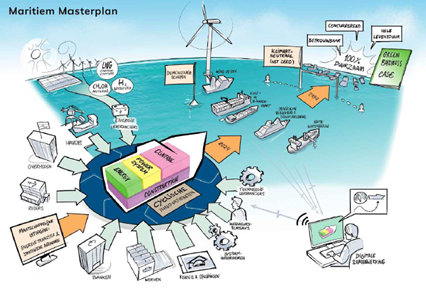
Eleven years back, in 2022, we embarked on an incredible journey. That was the year we planted the seed that developed into our AI-software for ship hull engineering. Personally, I find it hard to imagine how we ever managed without it. Where are we now, and how did we get there?
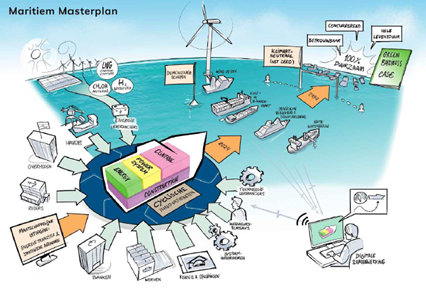
Fig. 1: 2023: Maritime Masterplan. Complex? Mwah……! AI Needed? Mwah…..!?
What motivated us to totally re-imagine our workflow? As engineers and designers in 2022, we needed to be on top of all design requirements and rules. A huge pile of data to keep track of, and we did so by going through spreadsheets, databases and text documents.
We had to keep track of so many different rule sources. Our own working standards. Classification rules, flag rules and client specifications. To begin with, it was complex to make all data needed available at the right time and place. And when we had everything we needed, there would be conflicting information more often than not.
Sometimes decisions were made based on one specific source of rules, while other rules were neglected without realizing. Sometimes specifications were updated, but not available at the right time at the right place, which led to high rework costs and loss of time, when it became clear crucial rules were neglected.
You can imagine a huge slice of our time went into this. Knowing that even a little mistake would be costly to correct, made our work quite stressful and mentally draining. Anyway, chapeau for those exceptional people who did it back in 2022!
We were convinced we should be working smarter. Nevertheless, we thought long and hard before starting the development of the MasterShip AI-tool. What were we getting into? We realized the impact could be big. Bigger even than the move from 2D to 3D engineering that had taken place in the 90’s. But as big as it proved to be?
Looking back, it was one of the best decisions we ever made. Nowadays, our AI-system keeps track of all rules and requirements – in real time. Does that mean we never have to think about it? No, we still do. But only once: when we update our rule base with new developments. That’s it!
No more searching through a collection of sources! The AI-software will evaluate information exactly when needed, judging which rules should prevail above others. Using our tool makes it virtually impossible to lose track of requirements or overlook rules.
Very important: we remain in full control over the in- and output. When we started this project in 2022, some people were apprehensive about AI. They expected it would take over control of design processes in such a way that users were unable to follow what was happening. Also, some people feared that there would be little work left to do for specialists.
There were parallels with the automation of factories and introduction of CAD/CAM in the 20th century. In that period, people also thought these developments would put many out of work. What happened was the opposite. Automation and CAD/CAM brought new and better jobs, increased product quality, improved work conditions and increased wealth.
I reckon with AI, it won’t be any different. If I look at our AI-software, I can vouch that our programmers are in full control. The software does not make actions it isn’t programmed to do. It also supplies users with clear reports about considerations and decisions. As a user, you can always check what is happening, and override decisions when you feel it’s needed.
We control the input, we control the programming, so we also control the output! And now in 2033 we can focus our attention on further automation of the ship design, engineering and building process. The development will continue, and the software will improve further!
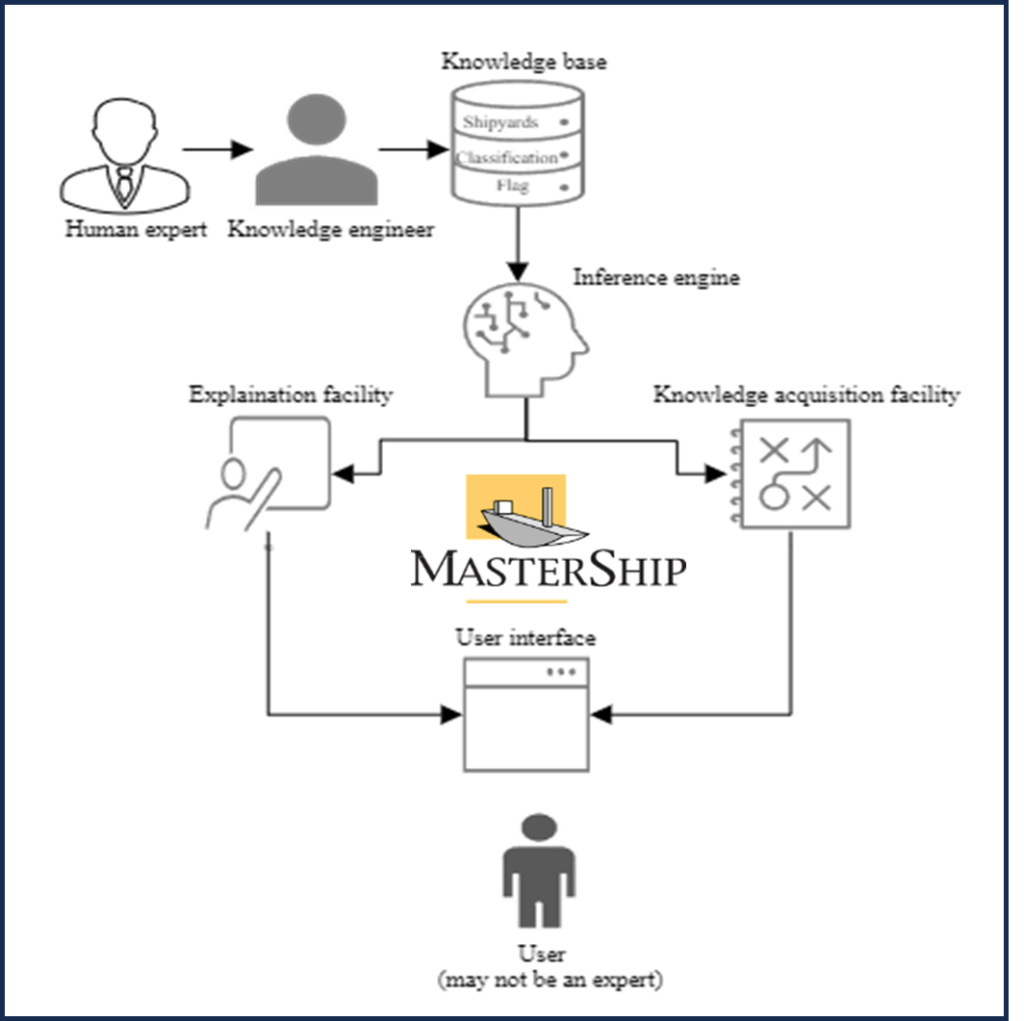
Fig.2. MasterShip AI; What if the user may not be an expert?
We saw early on: AI delivered! But of course, we had to learn to work with it. We had to be persistent. It was hard to imagine that this new system could store next to all requirements and rules – let alone all of MasterShip’s shipbuilding knowhow.
Eleven years ago we had a pretty good system to keep track of our knowledge and company standards. First we stored it in spreadsheets, databases and text files. Around 2022 we implemented an advanced Wiki system, making all information accessible via one interface.
Then still, it could be difficult to use the right rules at the right moment and situation, because the data was not integrated in the CAD/CAM software. This proved especially problematic when training new people. Despite our professional onboarding system, it remained a real challenge to retain and be aware of all the information. Completely understandable, of course.
Now, with our company standards and working methods loaded into the AI-tool, we do not have to look over their shoulders so much, knowing that they will be provided with relevant information only at exactly the moment they need to be aware of it, within the MasterShip software they are already working in.
I am not claiming that AI made mistakes a thing of the past. But I can state that the amount of mistakes are drastically reduced. And what is almost magical to me: the mistakes we do encounter, are utilized to improve the software. AI is self-learning, and we can add new rules that will be taken into account for the next project. It looks like our project evaluations 10 years ago but better! Secured. Every user of the software can use it straight away.
Another useful feature is that we can adapt a shipbuilding project for different shipyard standards. For example: the size of the shopfloor, area for section storage, hoisting capacity, maximum length for folding plates, maximum size for bending plates, industrial plate and staff sizes, available stock, and so on. Our AI software for the detailed and production design will deliver specific output depending on the yard information we loaded.
I will share an experience. Our project P1545 was built in a shipyard in Turkey. The second build number of the same design, was built in Canada. This meant that the whole set of yard standards had to be updated.
Starting from the basic design, we checked if the detailed design needed to be adjusted to the new yard standards. Within two hours the AI-system indicated that we needed 8 updates in the detailed design. A few of them could be executed automatically. Two we had to solve manually. The biggest advantage of the AI-system was in the next step, from detailed to production design. The changes needed could be executed fully automatically in just two days.
Another nice example: a recent retrofit project. For a 80m supplier with nitrogen propulsion, we had to replace the entire propulsion module, including the energy storage, transport and transition on board. Reason being the newest 2033 GGP (Green Gas Propulsion) system which had to be installed.
The AI-systems that were used during the Model Based System Engineering process of the designer, stored not only the metadata but also all of the functional design boundary requirements of the complete nitrogen propulsion module on board for all interacting other ship modules.
We replaced the metadata and the boundary conditions of the old nitrogen propulsions system with the new ones for the GGP propulsion system. This, together with the availability of all other actual rules sources and boundary conditions in the AI software, saved 40% of the total engineering and replacing time, and cut 30% of the costs.
Just two examples that underline the progress we made by investing in AI. In 10 years’ time, we cut 30% of the engineering time needed, 20% of the building time and 25% of the overall costs. We do our work with more ease, making less mistakes and producing higher quality. Anyway, chapeau for MasterShip AI now in 2033!
If you have any thoughts or questions please contact us.
Kind regards,
Jacques Hoffmans
+31 6 52 52 08 80
jh@mastership.nl
Tufail Shahzad
+31 6 84 01 80 90
ts@mastership.nl
www.mastership.nl