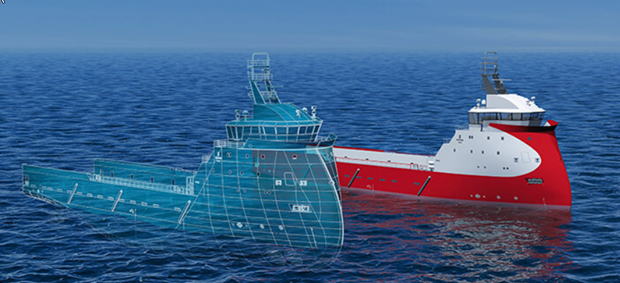
Picture: article Digital twins and sensor monitoring by DNV, Maritime Impact
Also presented at:
2021 International Cruise and Yacht Design Education & Industry Cooperation Platform Summit Forum, 11-12 December 2021, Wuhan University of Technology
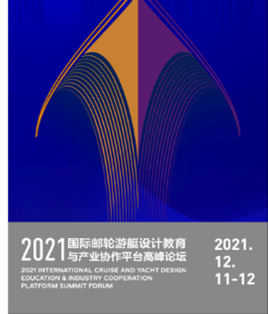
Industrial revolutions:
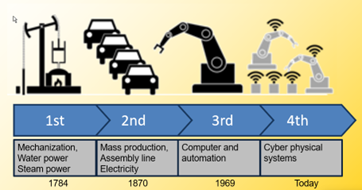
Actually we are in the 4th industrial revolution. The earlier three can be seen as 1st , the mechanization revolution (1784….), 2nd the mass production and electricity (1870-…..), 3rd computerization, digitalization (1969……) and now 4th the cyber physical systems Also called Industry 4.0 or Smart Industry (today……).
Note the duration between 1 and 2 and 2 and 3 is around 100 years and between 3 and 4 is only 50 years.
Facing these industrial developments it is clear that the next one could never be started without the preceding one! But could we have predicted the next one at the start of the preceding one? Can we now predict the 5th Industrial revolution? It is here where we need visionaries. Who knows it will be involved in energy or water.
The products from the 3rd industrial revolution like computers, automation and digital science offer now opportunities as Cloud Computing, Internet of Things, Virtual and Augmented Reality and Artificial Intelligence. The opportunities of combining items of these 4th industrial revolution are unimaginable.
Never thought I would ever write this down. After starting as an entrepreneur after my graduating in shipbuilding, I have had moments that I thought “And when we have developed this and that, what is next? Will there be a next thing to develop?” Now I say it is a never ending story and unimaginable what we are facing. Which makes it even more interesting.
Critical note:
Most Industry 4.0 initiatives are early-stage projects with a limited scope. The majority of digitization and digitalization efforts, in reality, happen in the context of third and even second industrial revolution technologies/goals. This is also the situation for the digital twin principle.
Of course there or also complex social and ethical sides to these new developments. Not to forget. But I leave it out here.
Our viewpoint as MasterShip.
At MasterShip we are specialized in making 3D virtual models of ships. With the goal to make building more efficient. Unless still important it is not the challenges anymore to make just fitting parts for steel hulls, for pipes and for interiors separately. But the challenge is to combine these disciplines in a fitting total. To twine the disciplines into each other during the design, engineering and building of the boat. And this twining will result nowadays in a digital copy of the real virtual vessel to be build, a digital twin. Twining into a twin. Thanks to the English language, in Dutch this was not possible.
But this digital copy in between engineering and building is just the starting point of what is meant with a digital twin.
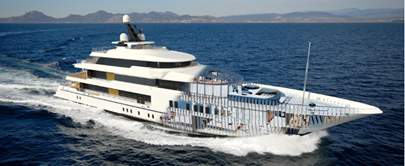
Definition digital twin
Definition: “A digital twin is a virtual representation that serves as the real-time digital counterpart of a physical object or process during the lifetime of a product.”
So indeed the digital copy in between engineering and building is just the starting point. After this it really starts. The new ship will starts to be used and will start to change. Meaning the starting twin situation will disappear. Unless we will maintain it. As the beginning of the lifetime of a ship the digital twin needs to be copied to a real physical product, but after that is done and as soon as the real ship will be used it is the other way around: the real physical ship has to be copied back to a digital twin! And for that we will need a digital “thread” between both! In fact many “threads” because we like to keep track of all systems and the ship itself.
This Digital Thread creates a loop between the physical product and the digital twin. This means we need a data-driven architecture that links together information generated from the product and all sub systems during the product lifecycle and is envisioned to be the real-time primary or authoritative data and communication platform for a company’s products at any instance of time. We could call it the maintenance dashboard.
Data transfer opportunity’s
For the shipowner
For the shipowner not only his start investment but also his costs of ownership are leading for his business model. With the digital twin system he can keep track of the conditions of his whole ship including all systems. Yes indeed, capex (CAPital EXpenditures) versus opex (OPerating EXpenditures).
The digital twin can be used for monitoring, diagnostics and prognostics to optimize asset performance and utilization. In this field, sensory data can be combined with historical data, human expertise and fleet and simulation learning to improve the outcome of prognostics. Therefore, inside the maintenance dashboard, complex prognostics and intelligent maintenance system platforms can use digital twins in also finding the root cause of issues and improve productivity.
So wee can find the optimum situation to find the best balance between his up time and maintenance costs.
Digital twins do not only have a right to exist for costs cutting. They will also learn us about the relation between the captured data and the consequences for the maintenance logbook. Next to direct cost cutting for the actual ship it will also deliver information to improve his next ship.
For the shipyard
Digital twins offers the possibility to deliver an efficient ship that will optimize the total costs including maintenance costs for the shipowner. This should be an unique selling point for the shipyard.
It was told to me by shipyard managers that they could follow their ships via their mobile phones. If G-forces or say oil temperature reached certain values alarms will go of. So when a few days later there comes request for certain repairs they are not surprised anymore.
Of course there will be costs involved in the technical monitoring. In fact most systems are already equipped with all kind of sensors and transmitters to get real time information at the system control or at the bridge of the ship. Within the digital twin principle this information must be transferred real time to the digital twin maintenance dashboard. This can be on board at the system control or at the bridge of the ship as well as or also at the head office of the shipping company. And even direct at the office of the system supplier.
For the actual status
We already have a very well developed sensor and chip technology. So getting the information is not really new. We can collect data about:
- Ship behavior: data like speed versus propulsion power, ship movements and involved G-forces
- System functioning and behavioral data: such as oil pressure and temperature, up time versus downtime, energy use, vibrations, noise, temperatures and others. Functioning and behavioral data can also be taken from the hull by sensors that will give information on the plate thickness on the positions where classification requires this. Also scantling stress can be monitored at critical positions.
- Environmental conditions: like humidity and temperature of air, like seawater conditions, like weather conditions.
Data can be read and relations between data and ship performance and ship maintenance can be stored and used for new design developments. The reliability of the data will be good enough. But the reliability of the whole systems used from sensors to communication to receivers might still be doubtful. But most certainly this will mature and become also reliable.
Also in domestic environments (as well home as yacht/ship domestics) we already have many advanced systems to control systems like heating, lightening, doorbells worldwide via mobile phones.
For better understanding please link to next movie by DNV.
Digital twins and sensor monitoring – DNV
Challenges
A ship is complex assembly of many systems. We need to set up the Digital Thread between all of them to have real time information about the status of these systems.
So yes, the challenge now is to design this digital platform, the maintenance dashboard, based on the digital twin that presents the overall results about the conditions of all systems and the ship itself.
Based on several other attempts for digital standardization I would say skip the effort to try to get all systems in the same software tool. Let every designer and supplier of the ship and of systems of the ship makes his own system based digital twin. Then for the shipowner it seems useful to use a software system that can assemble all the information into one system and make needed analyses on this assembled data.
The level of automation and completeness for all systems here can be decided for each situation and involved requirements.
System approach Digital Twins:
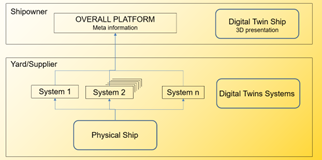
Digital twins can save money on maintenance, on insurance, increase the up-time for ships and can give input for developing better ships and better shipbased systems in the futures. It should be the responsibility of each system developer/OEM developer to keep track of the functioning of his systems on board.
It is up to the shipowner to decide on which data and information he wants to have available for his asset management
- Ship behavior
- Hull functioning and behavioral data
- System functioning and behavioral data:
- Environmental conditions:
Advanced ways of product and asset management comes within reach with the availability of a real time digital twin during the lifetime of the real ‘thing’.
If you have any thoughts or questions please contact us.
Kind regards,
Jacques Hoffmans
+31 6 52 52 08 80
jh@mastership.nl
Tufail Shahzad
+31 6 84 01 80 90
ts@mastership.nl
www.mastership.nl