One of the challenges in ship repair is fast action. Every day of inactivity is revenue lost for the shipowner. Traditionally, builders start cutting metal on day one. We let the builders wait. To take pictures? Well, it’s a little more sophisticated: to make a 3D-scan.
When repairing damage the traditional way, builders re-shape the hull with extraordinary skill, continuously measuring, cutting and shaping metal sheets. The result is an artful patchwork of metal. It takes a lot of time, but it does the job.
Shipyard de Schroef is a specialist in repair. When a ship came in with significant bow damage and no drawings, De Schroef’s Huib Kuiper reached out to Jacques Hoffmans of MasterShip. The two had talked before about innovating repair work. Now the opportunity came to put ideas into practice.
The idea was to make a 3D-scan of the ship, realising a digital model of the damaged hull to use in MasterShip Software. For the scanning technology, we partnered up with Geomaat. Geomaat has extensive experience applying 3D-scanning technology to monitor deformation of buildings and infrastructure. Recently they expanded their activities to the shipping industry.
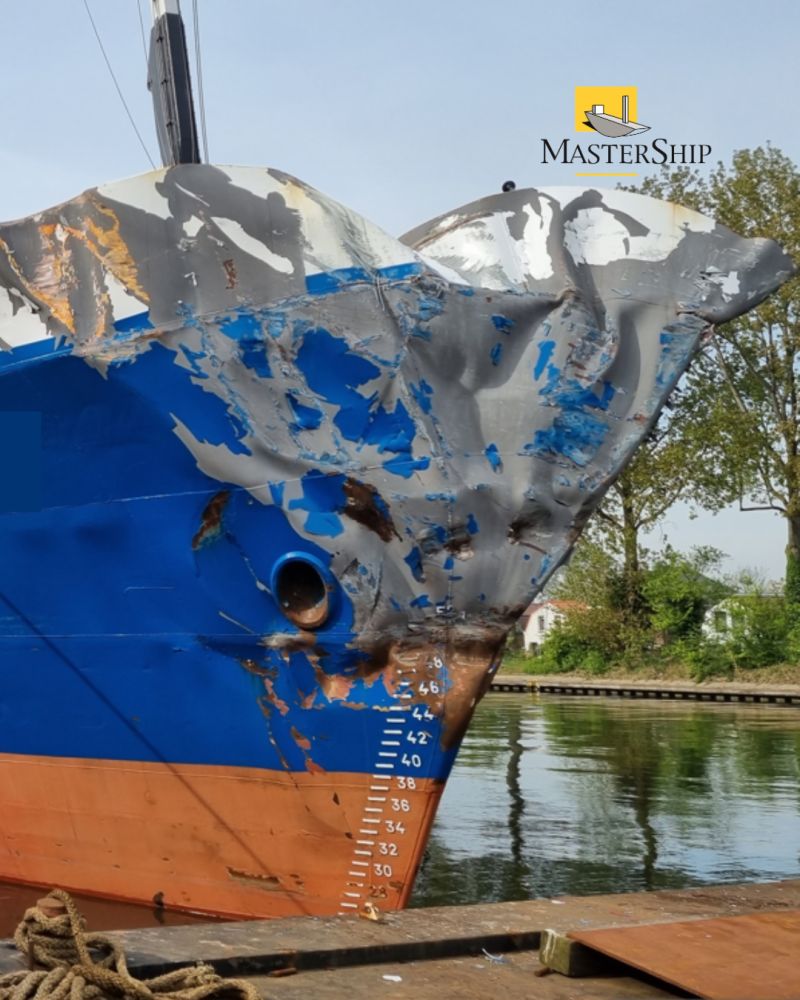
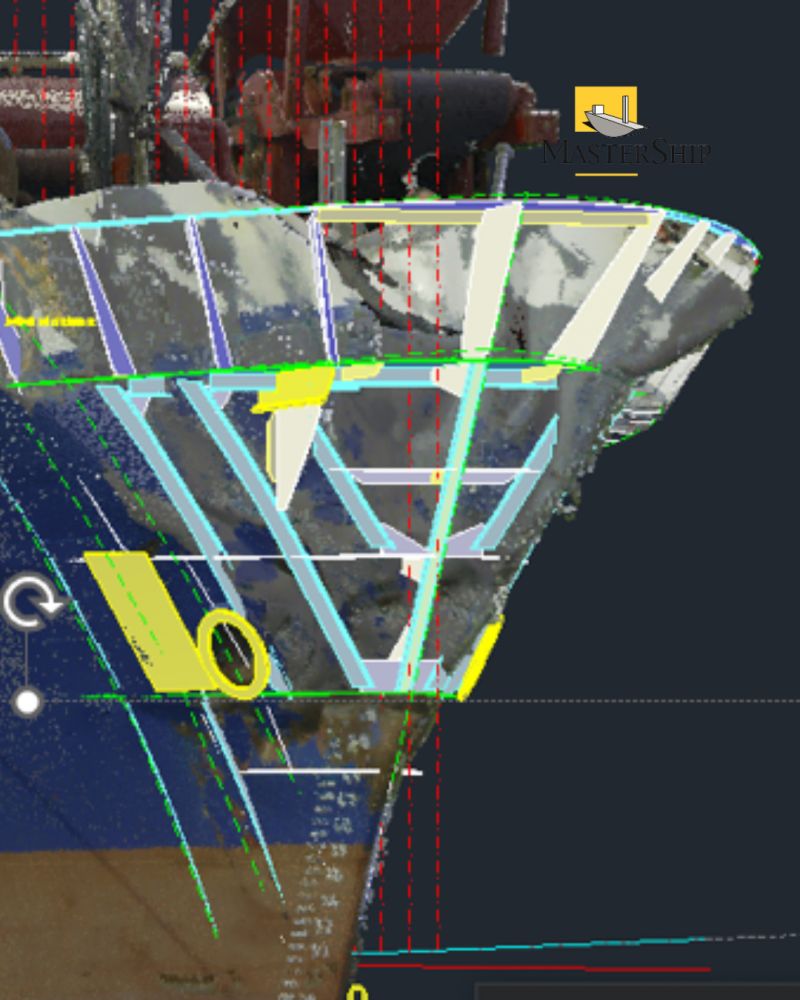
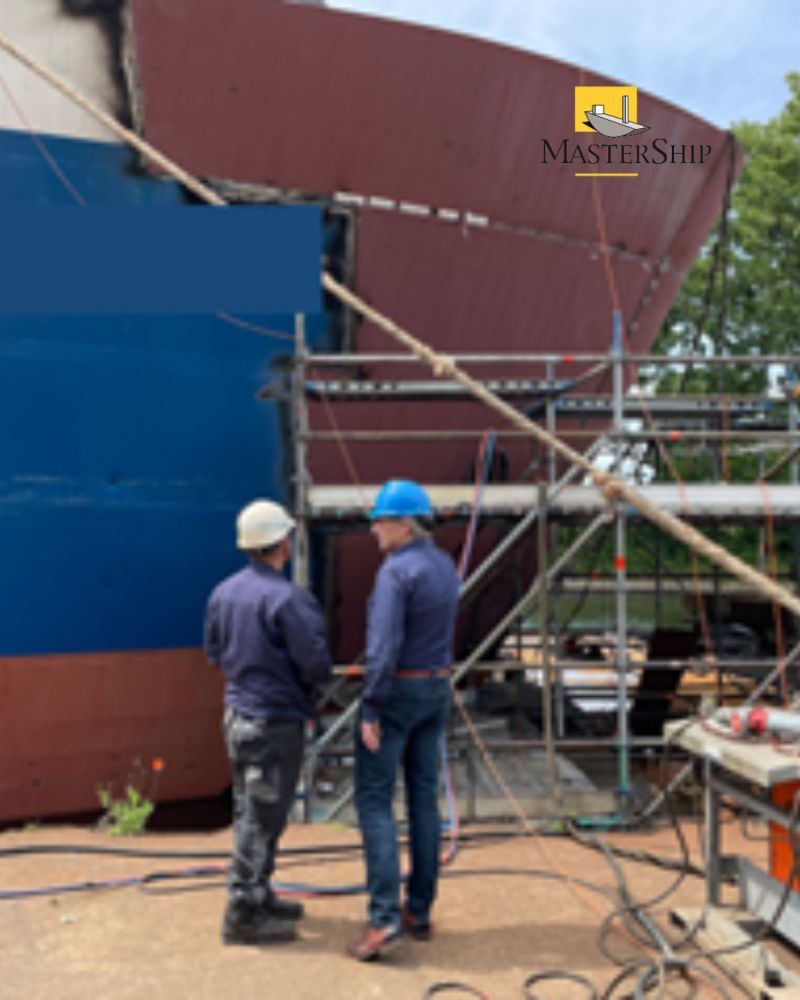
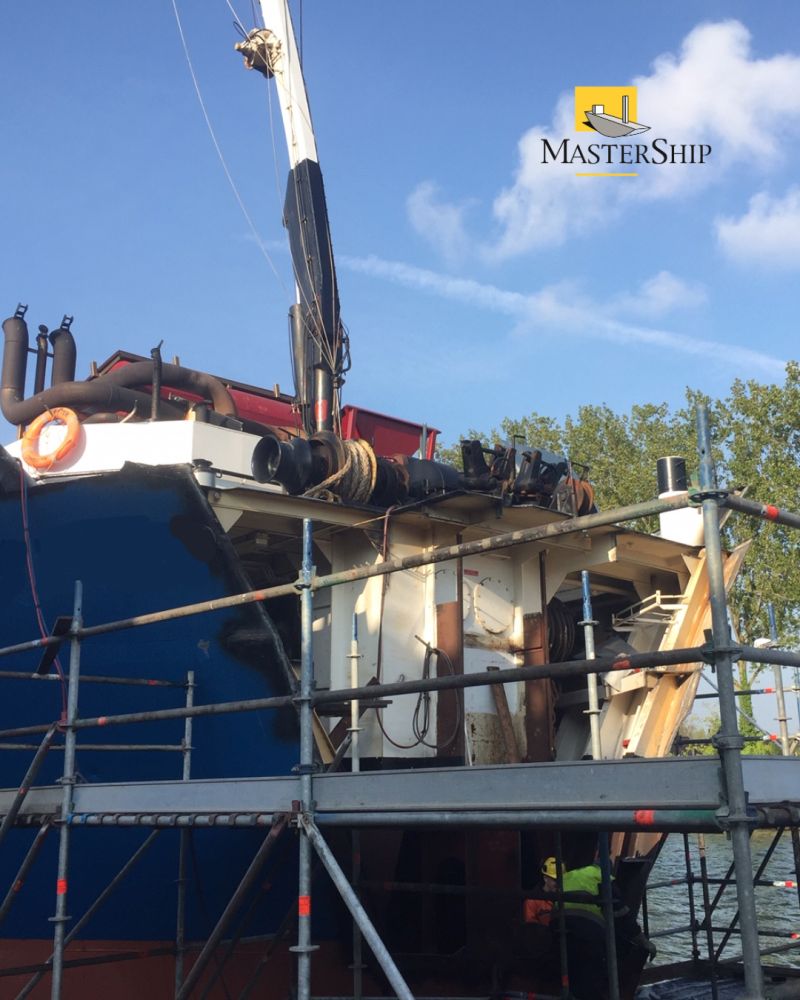
First Geomaat scanned the ship. Then MasterShip digitally designed a new hull shape to replace the damaged one, and made a 3D construction model. This way, builders from De Schroef were able to work on the repair as if they were building a new ship. In the end, we saved a significant amount of time and material.
If you want to know the ins and outs:
1. Geomaat started with a 3D laser scan of the damaged part plus 10 metres beyond the damage line.
2. We made a surface model of the scan data in CAD MasterShip Software. At the same time, builders at the shipyard started cutting off the damaged hull.
3. Huib Kuiper managed to dig up hard copy construction drawings. Pretty impressive considering the ship was built in 1993.
4. We used all information we had – shape, cutline and construction – to design a 3D construction model of the replacement hull in CAD.
5. MasterShip Software generated the production information such as hull plate expansions, shaping moulds, purchase lists, and nestings. Same as building a new ship!
6. At De Schroef, builders were able to organise the numerical cutting, the shaping of the double curved hull plates, the bending of the HP frames, and – last but not least – the assembly.
We finished an especially neat repair job in less time and with less gross material than it usually takes.
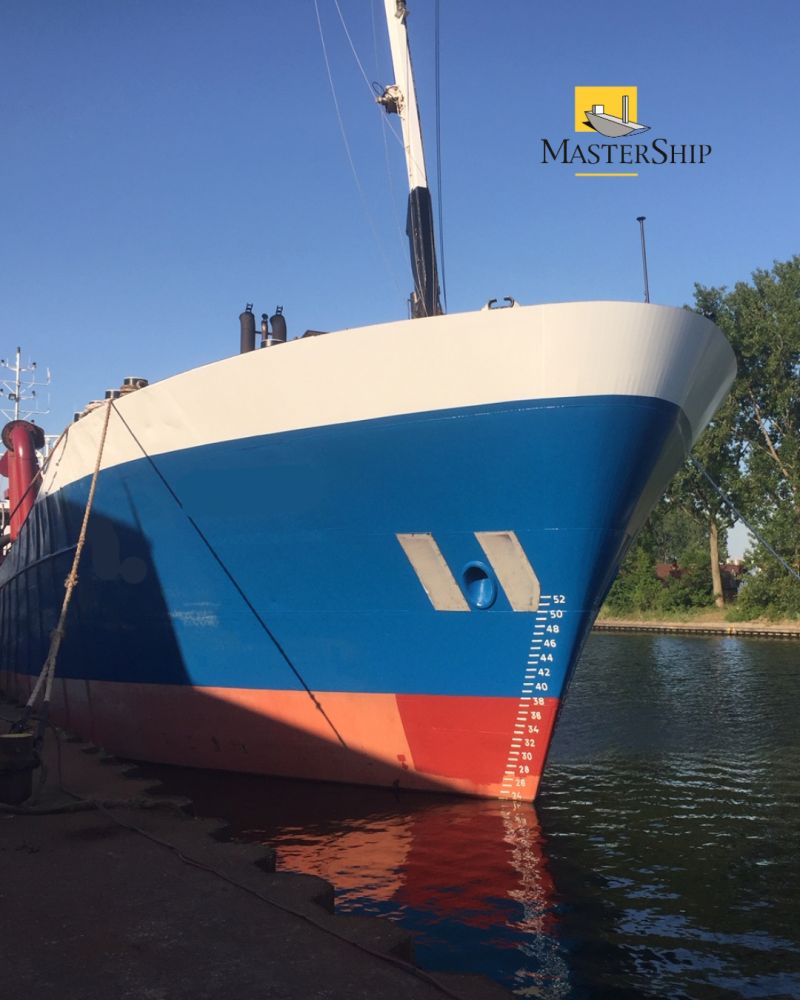
We would like to thank Scheepswerf De Schroef, for the opportunity and the collaboration, and Geomaat B.V. for their valuable input. Working as a team we figured out a more efficient way of ship repair and we gained a great deal of practical experience in the proces. We are looking forward to the next project together!
Jacques Hoffmans
T:+3140 3400 550
E: jh@mastership.nl